White Dwarf Combustion Chamber
Overview
The White Dwarf combustion chamber uses a water-cooled jacket, with a graphite nozzle. The cooling channels are cut into an off-the-shelf copper tube using a CNC machine. The outer walls of the cooling jacket are made of stainless steel and are welded together.
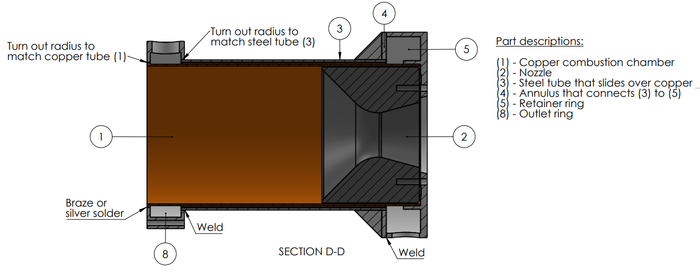
Resources
Engineering Drawings
2. Nozzle
8. Outlet Ring
9. Injector Face / Test Stand Mount
Water Pump
The engine uses an electric water pump to feed the cooling jacket, on a closed loop system. The water that leaves the cooling jacket returns to a main reservoir, where it is recycled so that the cooling jacket can operate indefinitely. This is useful for cooling the combustion chamber, and especially the nozzle, after engine shutdown, since the nozzle may act as a large heatsink. Post-shutdown, it may be possible for the nozzle to transfer sufficient heat to the metal components to damage them, if they were left uncooled.
The pump used is a Pentax CR 75, 230 V single-phase electric pump, which provides just under 1 kg/s of water flow rate (measured experimentally).
Copper Chamber
Made of copper due to it's high thermal conductivity, which significantly reduces the thermal stress across the walls as well as the wall temperatures. If steel was used, the thermal stresses would be much higher, and would outweigh the gain received from steel's higher yield stress.
Temperature and pressure drop predictions were generated using Bamboo, and the results are available on the simulations GitHub page.
Nozzle
The nozzle is made of graphite, and was manufactured by Tokai Carbon Europe. It contains 16 holes that will contain M5 x '3D' helicoil inserts, allowing the nozzle to be pulled into the retaining ring, whilst simultaneously compressing the graphite gasket in between the nozzle and retainer ring. This graphite gasket is used to seal the leak path between the nozzle and retainer ring.
Graphite thread failure calculations are available on the simulations GitHub page. Extra 'samples' of the graphite-helicoil threads were ordered, separate from the nozzle, so they could be tested until failure experimentally. This provided useful data to ensure that the threads on the nozzle were not overtightened and damaged when it came to tightening bolts into them.
Retainer Ring
The retainer ring is manufactured from a single large piece of stainless steel billet. It has an inlet for the water coolant, and is brazed to the copper jacket, and welded to the rest of the steel components.
Triangular gusset plates were added between the retainer ring and the steel outer tube, after an FEA analysis revealed a stress concentration at original (circumferential) weld point between the two. The gussets are intended to increase the weld length and reduce the risk of failure, which would arise from the combustion chamber pressure pushing the nozzle against the retainer ring.
Steel Outer Tube
The steel tube that encloses the copper fins will slide over the copper, and is not connected to the copper directly. It is intended to be a custom-made welded stainless steel tube, manufactured in the Dyson centre.
Outlet Ring
The coolant outlet ring increases the water flow area from the channels to the circumferential path it that must be taken to reach the outlet pipe. This increased flow area reduces the flow velocity, thus reduces pressure losses in the coolant outlet ring.
The outlet ring also contains 19 x M4 through-holes, to enable the injector face to be pulled against the outlet ring. A graphite gasket is present between the injector face and outlet ring to prevent combustion gas leaking out of that leak path.